Australia's main iron ore exports may not work with green steelmaking. Here's what we must do to prepare
- Written by Tessa Leach, Senior Analyst at Climateworks, Monash University
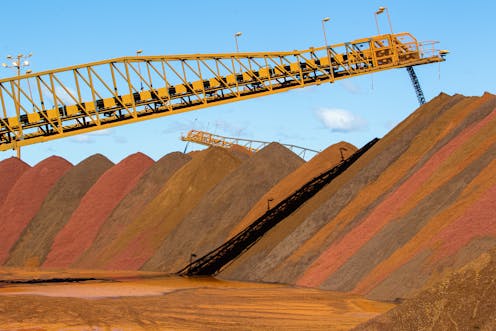
Making steel was responsible for about 7% of global greenhouse gas emissions in 2020. That’s because steelmakers in countries like China, Japan and South Korea have long relied on fossil fuels like coal to make steel in blast furnaces.
But change is coming, as the world works to decarbonise. Researchers and steelmakers are exploring new ways of making steel without using coal.
If the move to green steel gathers speed, Australia could be left behind. That’s because even though we’re the world’s largest exporter of iron ore, some of the new techniques rely on ore with a higher purity than we currently export. Coal exporters could also lose income, as we’re the largest exporter of the coking coal burnt in furnaces using current technology.
To avoid this, we should plan for a green steel future. Our recent report on opportunities for Australian industry to decarbonise suggests this is possible. Australia can make the transition to green steel and remain a major global player.
Why would Australia be affected by a shift to green steel?
Emerging steelmaking technologies are well along the path to development. Sweden produced the first batch of steel made without coal in 2021.
This steel was made using a direct reduced iron-electric arc furnace process, which can be powered with renewable energy and green hydrogen. While the pilot schemes are promising, this technology could take until the late 2030s to be available at scale.
The problem for Australia is this approach needs high purity ore. At present, the bulk of our iron ore exports would simply not be compatible, as there are too many impurities.
Australia exports two main types of iron ore: hematite and magnetite.
Hematite is mined in Western Australia’s Pilbara. It’s a naturally higher-grade ore (56–62% iron) and makes up almost all (96%) of our exports.
Magnetite is a lower grade ore (25-40% iron) which needs extra processing. This processing, however, produces ore with more iron content, fewer impurities and less waste rock (known as gangue) than hematite.
It’s also, as the name suggests, magnetic. That makes it possible to efficiently separate iron from waste rock using magnets.
Why does this matter? Because this processing converts lower grade iron ore into a product compatible with direct reduced iron-electric arc furnace technology.
You might wonder why it’s important to get rid of waste rock. Doesn’t it slough off in the furnace? In a traditional blast furnace, this is true. But in the direct reduction process, the iron ore doesn’t actually melt. And the next step – the electric arc furnace – can’t handle too many contaminants.
Hematite or magnetite?
This leaves us with a predicament.
Our major iron ore export, hematite, won’t be able to supply green steelmakers using one of the leading technologies. But our much smaller ore type, magnetite, could.
If we develop new methods of processing hematite to allow it to be used in green steelmaking, we could keep current mines open and preserve existing markets. But it would mean significant research and development to make possible commercially viable methods.
The other option is to accelerate mining of magnetite, because processing this kind of ore is well understood.
Some Australian miners are already heading down this path. Fortescue’s Iron Bridge magnetite project in the Pilbara is scheduled to begin production this quarter.
Magnetite is also recognised as an opportunity in South Australia, given it makes up 90% of the state’s ore body. The state government has set a target of 50 million tonnes per year by 2030.
To ensure expanded mining of magnetite is sustainable, we need strong benchmarks to limit emissions and broader environmental impacts from new mine facilities.
That’s because the actual mining of iron ore is an emissions-intensive industry, given it relies on heavy machinery. But our modelling shows there are pathways to progress here too, with electrification and fuel switching.
Are other green steel techniques better suited to Pilbara ore?
The direct reduction method being pioneered in Sweden isn’t the only way to clean up steelmaking.
We looked at a range of potential low-emissions steelmaking techniques, some of which could make use of Australia’s existing hematite exports.
Australian steelmaker Bluescope and multinational miner Rio Tinto are exploring another method, using direct reduction to get rid of oxygen, melting the ore to remove impurities, and then using a basic oxygen furnace to make steel. This, they hope, will let them keep using Pilbara hematite ore.
Other emerging steelmaking techniques, such as electrolytic steelmaking, should also be developed to ensure there are plenty of options for the use of hematite in zero emissions steelmaking in the future.
Fortescue Future Industries recently announced they have succeeded in producing zero carbon iron using an electrolyser and a membrane, but so far have not provided details of the process.
It’s hard to give concrete timelines for these changes, as a transformation at this scale will require coordinated effort. Each of these technologies requires significant investment and a massive build-up of reliable, cost-competitive renewable energy and green hydrogen production.
Planning and action is needed now
As you would imagine, steelmaking companies plan for their plants to last decades. This timeframe means decisions being made now will affect emissions in the future.
It’s vital Australia is prepared for the shift to green steel. We’ll need a national strategy to futureproof iron ore production, and iron and steel supply chain roadmaps to get suppliers, finance, consumers and decision-makers on the same page in working to take the fossil fuels out of industries.
Authors: Tessa Leach, Senior Analyst at Climateworks, Monash University